Weld precision taken to the next level
23 Jun 2015 by Evoluted New Media
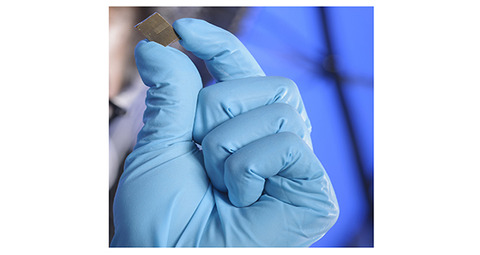
By using a new laser method, scientists have created the world’s smallest plastic weld.
Scientists at the TWI research organisation and the University of Cambridge used electron beam (EB) lithography and a laser to develop a new welding technique that can produce precise joints on 0.5-5µm scale.
To define weld position, the team used precise patterning of laser absorbtion dye on a thermoplastic surface, rather than an infrared laser which limits the control of laser focus. The team then used electron beam lithography to pattern the material and create welds with a width smaller than 10mm. The novel technique allowed the scientists to create joints between plastics on a much smaller scale.
Project leader, Ian Jones said: “This is a new process for joining plastics that has been developed by combining the capability of EB lithography and laser welding using infrared absorber coatings. Using laser welding alone it is not possible to make welds less than approximately 10 µm wide. However, if the infrared absorber coating is selectively removed in places first using EB lithography, then much smaller features can be welded. The welds are only made where the infrared absorber is still present. So there is an additional step involved, but welds smaller than 1µm wide have become possible.”
By using the plastic polymethyl methacrylate as a base material, the team tested their new method. The results showed that the laser technique can weld joints with widths of 1µm and channels of 5µm as well as smaller welds up to 0.5µm.
The team believes that the method could bring new applications for small scale analysis chips, chemical micro-reactors and electronics products.
“There is interest in making smaller bio-analysis chips, gas analysis sensors and lab-on-a-chip chemical reactors. They also need to be made at low cost. Use of plastics helps with this, and hence the need to precisely located and dimensioned joints. Adhesives are often used in these applications, but with very small sensors, there is a danger of blocking the channels or for contamination when using adhesives. This method offer an alternative,” said Jones.
Next, the team is planning on expanding their work to apply the process to other plastics.