A vehicle for change
7 May 2015 by Evoluted New Media
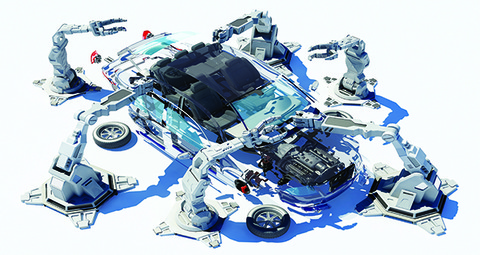
Graphene – wonder material it maybe – but there are many challenges to overcome before using it seriously as an industrial material. Here we find that some solutions are there, and by using them we could revolutionise the vehicle manufacturing industry
Graphene – wonder material it maybe – but there are many challenges to overcome before using it seriously as an industrial material. Here we find that some solutions are there, and by using them we could revolutionise the vehicle manufacturing industry
Over recent years, the popularity of polymer composite materials has significantly increased, particularly in applications where weight and durability are important factors for the final application.
There is currently a great deal of the demand for composite materials in industries where manufacturers are attempting to maximise the specific mechanical properties of their base materials. Strong and lightweight structures manufactured from composites can not only replace heavier and more expensive components, they have the potential to outperform traditional materials in multiple applications. Many industries including automotive and aerospace are showing considerable interest in developing new high performance composite materials to improve their commercial standing. This not only has significant impact in terms of the initial manufacture, it also has extensive implications in fuel consumption and emission reduction.
One considerable advantage to the use of composites in transport applications is the ability to manufacture complex parts which are not necessarily possible, or are at least incredibly difficult to fabricate, using existing metal production processes. These materials also offer incredible weight savings, without sacrificing strength or durability. The resulting structures can then be used to manufacture high performance vehicles which can outperform their metal based counterparts in terms of efficiency and structural integrity. In addition, due to the relative simplicity of production techniques, the manufacture of composite parts for transport applications is a great deal cheaper with considerable reductions in process costs and labour.
More attractive still is the possibility of improvement via the introduction of additives. Recent academic research and advancements in industrial manufacturing have demonstrated the benefits of infusing raw materials with particulate additives in order to enhance their most valuable properties. This research has itself spawned a plethora of innovative products to achieve the increasing efficiency and cost reduction targets currently faced by transport engineers.
For example, with a small amount of additive it is possible to create a protective coating that repels water which prevents the formation and build-up of ice on aeroplane fuselages. Electrically conductive coatings can also be engineered, that indicate fractures in the underlying structures and certain paints are now available on the market, that when applied to car doors, appears to ‘heal’ when the panels are scratched or marked.
When selecting an additive for a composite it is extremely important to bear in mind the improvements desired in the end product. For many years, reinforced carbon fibre has been a favourite for mechanical improvement in applications that require increased durability, while metals like silver are preferred for conductive composites. Whilst these materials have clearly demonstrated their potential in improving base properties, both are relatively expensive to source for production and manufacturers need solutions to overcome these challenges.
In the search for cheaper alternatives which offer equal or greater performance than traditional materials, researchers discovered a viable alternative in graphene. Stronger than steel and with a greater value of electrical conductivity than either copper or silver; graphene has a wealth of potential applications within the transport sector. Lighter vehicles with graphene composite frames have great promise in decreasing fuel consumption and production costs. There are also energy considerations to be made, as graphene’s superior conduction capability could vastly increase the transmission efficiency of electrical power lines for trains and trams.
Additionally, the use of graphene in pure or additive form has environmental implications, as it is an abundant and sustainable raw material, reducing the need to source rare and precious metals for the construction of vehicles and infrastructure.
Graphene is a complex material in itself and has many forms. Pure sheet graphene has remarkable in-planar strength and durability with unrivalled electrical and thermal conduction properties, making it ideal for electricity transmission applications. However, due to the difficulty in producing large, uniform layers of atomic thickness, sheet graphene is not yet available in dimensions suitable for industrial application development.
Graphene nanoparticles including graphene nanoplatelets (GNPs) and carbon nanotubes also demonstrate impressive mechanical and conductive properties, and are much easier to produce. Whilst their small size precludes them from use in pure graphene solutions, they do have considerable potential in the manufacture of graphene reinforced structures and components. By integrating small amounts of graphene nanoparticles into a base material, it is possible to manufacture enhanced materials with far greater mechanical properties than the raw constituents. However, the key to realising the full potential of any graphene reinforced composite, is a homogenous dispersion of the nanoparticles within the host matrix.
As raw graphene nanoparticles are essentially collections of inert carbon atoms with low surface energies, manufacturers experience great difficulty in achieving good distributions of the nanoparticles and therefore fail to forge strong chemical bonds between the graphene and other substances. Therefore, the full realisation of graphene reinforcement can only be achieved through functionalising the nanoparticles, in order to encourage better distributions and stronger bonding between the host and the additive. This prevents the formation of structural weaknesses which can easily cause fractures or deformation, providing uniform reinforcement throughout the composite.
Graphene functionalisation is achievable in several ways, however many of these methods have high costs, both financially and environmentally, which must be carefully weighed. One such method utilises chemical shocking, creating greater surface bonding capability via the use of acidic agents, though this approach has drawbacks. Aggressive acidic compounds have the potential to damage the nanomaterials thereby degrading the performance of the end product. There are also substantial environmental considerations to be made when utilising these agents as they must be disposed of properly in accordance with the EU Waste Framework Directive1. This in itself generates large additional costs to the functionalisation process.
The most promising functionalisation technology for the full realisation of graphene enhanced materials is the low temperature plasma process. It is a scalable process which is capable of not only functionalising graphene, but a wide variety of nanomaterials intended for the improvement of composites. Raw materials are passed through a low temperature plasma, thereby coating the surfaces of the nanoparticles. The new chemicals deposited on the surface of each particle increase the potential for effective chemical bonding, which in turn facilitates more homogenous dispersion within the host matrix. There are several additional advantages to utilising this technique; the functionalisation chemicals can be taken from a wide range of exotic compounds tailored to the needs of the application and which do not involve aggressive acids or wet chemistry processes. This ensures a high performance end product whilst also removing additional processing costs and avoiding the environmental considerations associated with other techniques.
The effectiveness of low temperature plasma processing has been confirmed by several recent studies investigating performance improvements in graphene enhanced composites. Aerospace Corp, based in California, added GNPs to an epoxy resin and found that the graphene additive increased the mechanical strength of the composite by 200% and the toughness by over 125% 2.
Another project, undertaken by the Cardiff School of Engineering at CardiffUniversity, investigated the effects of graphene reinforcement on carbon fibre. The study, conducted as part of the European Clean Sky initiative to develop high performance aerospace structures to reduce emissions and fuel consumption, expected that the dominant effects of the fibres would suppress any enhancements offered by the graphene additive. However, the research showed a 13% increase in compression strength and a 50% increase in compression after impact performance, an extremely significant result which has massive implications for existing carbon fibre technology.
With the material enhancements offered by graphene reinforcement, vehicle manufacturers now have the potential to design and build ultra-high performance cars, aeroplanes, boats and even spacecraft. Not only do graphene based composites already promise to outperform many of the industry’s preferred and traditional materials, but they can offer the manufacturer considerable savings on raw materials and even production.
The new generation of enhanced vehicles has great potential to create significant savings for the end-user, as lighter cars and aeroplanes will significantly reduce fuel consumption without sacrificing durability or even more importantly, safety. Furthermore, with lower emissions and the wider use of graphene as a raw material, the cost of industrial manufacturing on the environment can be considerably reduced.
The key to realising graphene’s true potential in applications for transport is in achieving homogenous dispersion of the nanoparticles within the epoxy matrix. Low temperature plasma processing offers the most effective route for graphene functionalisation and promises to yield high-performance composites which have the potential to revolutionise the automotive industry. The cost savings propose an extremely attractive option for manufacturers, while reduced fuel consumption and emissions represent significant advantages for consumers across the world.
References
- UK. European Union. European Parliament. DIRECTIVE 2008/98/EC OF THE EUROPEAN PARLIAMENT AND OF THE COUNCIL of 19 November 2008 on Waste and Repealing Certain Directives. N.p.: EU, n.d. Web. 9 Feb. 2015.
- Zaldivar, R. J. et al. (2014). Strength improvements in toughened epoxy composites using surface treated GnPs. Applied Polymer Science, 131(18): 9534-954
The author
Gerry Boyce is Managing Director of EPL Composite Solutions a subsidiary of Haydale Ltd