Are you moving on?
18 Apr 2013 by Evoluted New Media
Lab moves can be a genuine ‘once in a lifetime’ experience. Professional office and lab relocation specialist Mark Whitehead gives his us his ten step guide on how to survive the upheaval
1. Planning
It sounds obvious but the better the planning, the better the move. Generally lab managers and technicians are better clients when it comes to moving because they have methodical, analytical minds. As long as there’s enough time to plan properly the move should be a stress free experience for all parties with nothing left to chance.
It is advisable to get the key people from the lab and the relocation company together as early as possible in the planning process so that all parties fully understand and appreciate the move requirements, deadlines and specifics for the move. Compiling a comprehensive list of what needs to be relocated as early as possible ensures that the correct resources and materials can allocated – it will also highlight any areas of concern and will identify where third parties need to be notified or engaged with regards to the preparation / decommissioning of equipment etc.
The sooner you engage a relocation company the better as this allow them to add more value to your project in terms of advice and experience – they will have the time to be proactive rather than re-active which can ultimately save money.
Whilst the moving process will be generic, no two moves are the same and it is imperative that the relocation company fully understands any specific or unique requirements the lab may have.
Communication is the key during the planning element and it is imperative that the relocation company is kept in the loop with regards to any changes, additions or alterations. Keep meetings regular. Don’t wait for a problem to arise – move team meetings can be brief but effective in identifying progress and problems. Lab moves tend to have many involved parties, especially when it comes to moving specialist equipment. It may be that you have more than one contractor on site at any one time and access dates / times will need to be coordinated to avoid any issues.
2. Site surveys
The move team must conduct thorough surveys of the existing and new laboratories. During these site surveys the relocation company will consider the following:
- What needs to be move from where and to where.
- Access / egress at both existing and new locations. This will include assessing the relevant access points, lifts / stairwells and doorways / ceiling heights to ensure that this will accommodate items being moved.
- Parking arrangements at both existing and new locations – where off-road parking facilities are not available, the relocation company will need sufficient notice to arrange parking suspensions, dispensations and permits with the relevant local authority.
- The type of specialist equipment that needs to be moved and whether or not other third parties will be involved on the decommission / decontamination of the equipment prior to relocation.
- Whether or not other third parties will be on-site during the move programme, what their responsibilities are and timing.
- What chemicals, solvents, acids or other hazardous material may need to be moved.
- Whether or not fridges / freezers will be relocating and whether these need to be moved in a ‘live condition’ with contents intact.
- Assess the quantity and type of packing crates / materials required for the move.
- Agree packing / unpacking responsibilities.
- Proposed date(s) and timescales for the move – whether or not the lab will move over a single or multi-phase period.
Dimensions of larger furniture and equipment is critical, along with door widths and access routes to loading areas. For any multi-storey facilities lift size and/or staircase dimensions are also fundamental.
3. Contingency planning
The initial planning meetings and site surveys usually identify areas of concern or potential issues – which is when contingency planning comes into play.
Any specific requirements or concerns should be highlighted to the relocation company so that they can ensure that contingency plans are in place.
General areas on contingency planning would normally include parking / access and lift usage.
Unfortunately there are some things you cannot plan for, including the weather, but again an experienced removal company will be able to advise you any areas that may need to be considered in terms of contingency planning.
4. Meeting legislation requirements
The same stringent safety practices from the lab need to continue as chemicals and hazardous materials move from one location to the next. For moves where the public highway is used, a Dangerous Goods Safety Advisor (DGSA) is required by law to ensure that chemical and dangerous substances are transported safely and legally, including the correct placarding, labeling and documentation that may be required. The earlier the DGSA is appointed, the sooner any issues will be highlighted and costs minimized by finding appropriate solutions.
Generally, the removal company will be require a full list of the chemicals, solvents, acids and hazardous materials at least 7 working days prior to the move taking place, but again this should be provided as soon as possible to ensure that the DGSA has sufficient time to consider these.
The information should include as a minimum the following information:
- Description of chemicals etc.
- Quantity being moved.
- Confirmation on whether they are hazardous, flammable or toxic.
- Whether they are liquid or power form.
- How they are currently stored.
5. Information Technology
IT is a fundamental part of any organization and laboratories are no exception. Having adequate backups before a move are essential – any data stored locally should be backed-up onto a server or other external device before the move.
One of the most essential factors in any successful move is having IT and telecoms services fully functional for staff arriving for work on their first day in the new premises. For this reason it is recommended that IT is moved at the very beginning of a project, using a failsafe method for tracking each piece of equipment from one site to the other. This will ensure that equipment is made available for re-commissioning as soon as possible during the move programme.
An audit can ascertain what equipment is to be moved, when it is to be moved, who is responsible for decommissioning / re-commissioning this equipment (this is usually a service the relocation company can provide assuming that this is not being done in-house or completed by a third party) and where it is to be moved from. As part of the audit, any issues can be raised regarding inoperative/broken/damaged equipment and acted upon prior to moving to the new site.
Where insurance cover is being provided by the relocation company it will probably be a condition of the insurance that all equipment is ‘professionally packed / unpacked’ i.e. packed / unpacked by the relocation company in order for the items to be insured. This is something you should check with your relocation company.
Decommissioning
- Pre-move testing to check PC working properly
- Power Down
- IT equipment labeling and audit of equipment
- Disconnection of all IT and associated equipment
- Removal of toners, drums, ink cartridges from printers for safe packing
- Audit list check to ensure all IT equipment is accounted for and in working order
Relocation
All IT equipment should be wrapped and packed in crates specifically designed for IT or security roll cages if deemed more suitable. The crates should be labeled with their new location code prior to transportation in air ride vehicles to their new destination.Re-commissioning
- Check all items are fully accounted for in their new positions
- Connection of all power leads, keyboards, mice and any peripherals.
- Recording new patch numbers.
- Reinsertion of printer trays and removal of transportation protection.
- Replacement and reconnection of leads
- Replacement of toner and drums cartridges
- Checking diagnostics and network on powering up.
- Self-test routines
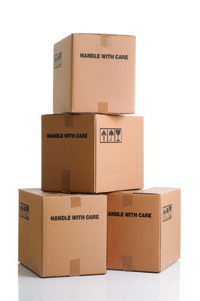
6. Refrigeration Equipment
If fridge contents are to be moved in a ‘live condition’ within the refrigeration unit, they must be packed and secured prior to relocation. Plenty of bubble wrap will usually suffice and would normally be provided by the relocation company. Contents should be tightly packed to ensure that they cannot move. If weight is an issue, for example if the fridges require being carried up or down staircases, it may be prudent to plan for using a spare fridge or polystyrene chill containers to chill the contents until the fridge is down to temperature in its new location.
Your relocation company should be able to provide a generator vehicle that has capacity for ensuring the fridges remain powered up during transit thus ensuring the temperature levels are maintained and the contents do not become compromised. Some removal companies will also be able to provide generator vehicles that also have separate chiller units in which loose items / chill containers can be stored during transit.
The relocation company will be able to advise whether a generator vehicle is required and assess your requirements.
7. Freezers
In an ideal world, the freezer contents are secured, the freezer is disconnected from the mains (by an electrician if necessary), moved directly onto a generator vehicle (see Refrigeration Equipment section above) where it is then connected to a power supply to ensure that the correct operating temperature of the freezer can be maintained. At the destination, the freezer is disconnected, transported directly to its final location and reconnected to the power supply (by an electrician if necessary). In some instances, larger freezers will not fit into lifts, and may have to be carried via the stairs, or may not fit through / under doorways. Either way, the freezers may need to be tilted or carried at an angle and this is where contingency planning comes into play. Manufacturers guidelines will differ, but in some cases a fridge or freezer will need to be left for 24hrs before re-connecting to power to allow the gases to settle to ensure that the equipment operates correctly and does not compromise the contents. Where the freezers need lifting, contents may need to be removed due to weight constraints. Either a new or temporary freezer can be used for decanting purposes or polystyrene cases with dry ice can be used to keep the contents at the correct temperature. It is also possible to use generator vehicles with chiller compartments as detailed earlier. Care must be taken to select the most cost effective solution that meets the temperature requirements depending on the sensitivity of the materials to ensure that they are not compromised during the relocation.
8. The three Ds: Disconnection, Decommissioning and Decontaminations
Timing and coordination is the key to a successful move, particularly with regard to moving equipment. With service companies usually responsible for the disconnection, decommissioning, re-commissioning, reconnection and calibration of equipment, there can be several service providers involved, even on a relatively small laboratory move. This escalates the importance of timing and coordinating the number of people working in the laboratory on any given day to achieve shut-down on move day.
Prior to relocation the lab equipment will need to be disconnected, decommissioned and decontaminated (where applicable) prior to packing. Where necessary the decontamination certificates will need to be made available and attached to the relevant equipment from a Health & Safety point of view. For example, safety cabinets / fume hoods will need to have filters removed and will need to be decontaminated prior to removal.
9. Office contents
While typically easier to move than the technical elements, the conventional desks, chairs, filing etc. tend to get overlooked in laboratory moves.
Specialist crates make moving files and paperwork a much easier task and a well planned labeling and packing system can streamline the process.
Any items of furniture should be protected on the vehicles by the use of removal blankets and then strapped to vehicle tie rails using webbing or ratchet straps, depending upon the type, size and weight of the items.
Loading and off-loading should be made using a hydraulic tail lift, which ensures that the furniture is not lifted. Any furniture items needing to be carried up or down stairs should be handled by operatives who are experienced in this task and should take great care to observe the requirements of building protection and Health & Safety.
10. Recycling, clearance and disposal
After everything for the new site has been transported, there is usually a proportion of redundant furniture and equipment. Care should be taken to clear the items from site and make arrangements for their recycling or disposal. Some furniture and equipment may be able to be sold which can help offset the cost of the move. Alternatively items can be broken down into component materials and recycled. Certificates can be obtained to demonstrate compliance with Corporate and Social Responsibility policies. Lab equipment should be decontaminated and relevant certificates made available as these will be required by the recycling facility.
Having worked with laboratories across the country and many lab managers, I have learnt a huge amount about different requirements, but the two key ingredients for a successfully move are good planning and communication. In most instances, the only constant on a move is change.
Author: Mark Whitehead is the Commercial Director at Function Business Services. He can be contacted on 020 7138 3260 or by email on mwhitehead@function-online.com. More information about Function can be found at www.function-online.com.