Back to basics: particle characterisation
14 Aug 2012 by Evoluted New Media
Particle characterisation is a critical activity for industry and academia alike and the range of supporting analytical technology is advancing steadily. Here we look at the fundamentals of how to describe particles and at the strengths and limitations of some key technologies is intended to help put today’s choices in perspective
Measuring the properties of particles is an essential precursor to their control in order to produce materials that behave in the desired manner, whether particulate raw materials, finished products, or anything in between. Since the general definition of ‘a particle’ often extends to include liquid droplets and gas bubbles, particle characterisation is of interest to a diverse range of manufacturers, from those formulating dairy emulsions for the food industry to companies making metal powders for component engineering. Whatever the application, it is important to adopt an appropriate analytical strategy. Used effectively, particle characterisation adds value at many stages of industrial processes supporting the drive for market-leading product quality and cost-efficient processing.
In manufacturing and development, two of the most important particle properties are size and shape, even though microstructure, surface, mechanical and charge properties may all define product performance. Taking this as a starting point it is useful to consider how particle size and shape can be defined and the relative importance of different descriptive parameters, and what to consider when choosing a particle sizing technique for a specific application.
Particles are complex 3-dimensional objects and neither their size nor shape can be fully described with just a single figure, except in the case of perfect spheres. For particle size, the concept of equivalent spheres is often used (figure 1). This involves defining particle size as the diameter of a sphere with the same value of a certain property as the actual particle.
Particle characterisation is of interest to a diverse range of manufacturers, from those formulating dairy emulsions for the food industry to companies making metal powders for component engineering[caption id="attachment_29582" align="alignright" width="200" caption="Figure 1: Illustration of the concept of equivalent spheres"]
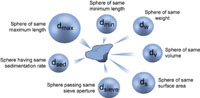
Many equivalences can be applied. While all are equally valid, some may correlate more closely with the behaviour of interest than others. Different measurement techniques use different equivalent sphere models and will not give exactly the same result for the particle size, making it important to choose a method that is well-suited to the application. For example, a technique that returns dsed, a diameter based on equivalent sedimentation rates, may provide more useful data for someone optimising a settling process, than one that reports dmin, a diameter based on minimum length equivalency.
The equivalent sphere concept works well for many types of particles but is not universally applicable. Needle- or plate-shaped particles, for example, have one dimension that is outstandingly different from their other dimensions. In the case of the rod shaped particle shown in figure 2, the dv, the diameter based on equivalent volume, would be 198 µm. If we instead define the particle as a cylinder of the same volume, this gives a length of 360 µm and a width of 120 µm and describes the particle in a more meaningful way.
Turning to particle shape, this too requires certain simplifications to make analysis and statistically relevant comparison feasible. Particle shape is often measured using imaging techniques that generate a 2-dimensional projection of the particle profile, from which shape parameters describing form and outline are determined.
Aspect ratio (the ratio of width to length) is routinely used to describe the form of a particle. It easily differentiates those possessing regular symmetry, such as spheres or cubes with an aspect ratio close to one, from more needle-like or ovoid types. Other parameters describing form include elongation and roundness.
The outline of a particle’s shape also provides information about properties such as surface roughness. Here a concept known as the convex hull perimeter is often used. This is the length outlined by an imaginary elastic band stretched around the particle image (see figure 3), and is used to define two descriptors of the outline of a shape:
- convexity = convex hull perimeter/actual perimeter
- solidity = area bound by actual perimeter/area bound by convex hull perimeter
[caption id="attachment_29583" align="alignleft" width="200" caption="Figure 2: Using cylinder rather than sphere equivalence can be more informative for needle-shaped particles"][/caption]
Finally for describing shape, some parameters provide an indication of both form and outline. Circularity is one and is defined as:
Circularity* = perimeter/perimeter of an equivalent area circle
*Sometimes defined as (perimeter/perimeter of an equivalent area circle)2 in which case it is referred to as HS circularity to avoid confusion with the above definition.
Circularity quantifies how close a particle is to a perfect sphere, and can be useful in analyses such as the wear on abrasive particles. Some care is needed in interpreting circularity data, since it cannot differentiate between changes in surface roughness and physical form.
It is all very well describing a single particle but samples will contain many, usually of varying dimensions. Analytical techniques address this by either reporting an averaged figure or generating a distribution. Distribution curves are presented in different ways with respect to the weighting given to individual particles. This depends upon the measuring principle being applied and can be a critical factor when selecting an analytical method.
Counting techniques such as image analysis produce number weighted distributions where each particle enjoys equal weighting, irrespective of its size. Shape distributions are therefore usually number weighted. This kind of distribution is especially useful when it is important to know the absolute number of particles – in foreign particle detection for example or where high resolution (particle by particle) is required.
[caption id="attachment_29584" align="alignright" width="200" caption="Figure 3: The convex hull perimeter provides a basis for comparing the surface roughness of a particle"][/caption]
In contrast, static light scattering techniques such as laser diffraction produce volume weighted distributions where the contribution of each particle relates to its volume – (size )3 (or mass where density is constant across the particle population). These distributions are important from a commercial perspective as they represent the composition of the sample in terms of its volume/mass, and therefore its potential monetary value.
Dynamic light scattering techniques are different again and produce light intensity weighted distributions where particle contribution is related to (size)6 making them extremely sensitive to the presence of large particles.
Figure 4 shows the impact of representing data in different ways. Converting from one type of distribution to another is possible but requires certain assumptions about the form of the particle and its physical properties. This is why, for example, a volume weighted particle size distribution measured using image analysis may not agree exactly with a particle size distribution measured by laser diffraction.
A first question when selecting particle characterisation technology is: which particle properties are most important to me? The answer is often size and shape, and this focuses attention on the issue of which instrument is most suitable for an application. While the data an instrument delivers is one aspect of this choice there is an array of practical considerations:
- What particle size range do I want to work over?
- Are my samples polydisperse and do I need a wide dynamic range?
- How quickly do I need to be able to make measurements?
- Do I need to measure at high resolution?
- Do I need to measure my sample wet or dry?
- How much money am I prepared to spend?
Further examination of a few of these techniques helps to crystallise understanding of the differences between them and their suitability for different applications.
Laser diffraction is widely used for materials ranging from hundreds of nanometres up to several millimetres in size. Primary reasons for its success are:
- Wide dynamic range;
- Suitability for both wet and dry measurement;
- Rapid measurement;
- Repeatability;
- High sample throughput;
- Calibration not necessary;
- Well-established technique.
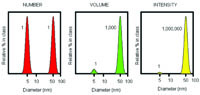
Furthermore, laser diffraction has made the transition into the process arena with a range of commercial systems now available for real-time continuous measurement in the plant environment.
Laser diffraction measures particle size distributions by detecting the angular variation in intensity of light scattered as a laser beam passes through a dispersed particulate sample. Large particles scatter light at small angles relative to the laser beam while small particles scatter light at large angles. Analysis of the angular scattering intensity data allows calculation of the size of the particles responsible for creating the scattering pattern, using the Mie theory of light. Particle size is reported as a volume equivalent sphere diameter.
Dynamic light scattering (DLS), sometimes referred to as Photon Correlation Spectroscopy (PCS) or Quasi-Elastic Light Scattering (QELS), is a non-invasive, well-established technique for measuring the size of particles and macromolecules in the submicron region down to below 1 nanometre. It is used to measure particles suspended in a liquid, such as proteins, polymers, micelles, carbohydrates, nanoparticles, colloidal dispersions, and emulsions, and offers a range of benefits:
- Size range ideal for nano and biomaterials;
- Small sample size;
- Fast analysis and high throughput;
- Non-invasive, allowing complete sample recovery.
Automated imaging is a high resolution direct technique for characterising particles from around 1 micron up to several millimetres in size. Individual particle images are captured from dispersed samples and analysed to determine size, shape and other physical properties. The key benefits of are that it enables the:
- Measurement of shape as well as size;
- Detection and/or enumeration of agglomerates, oversized particles or contaminant particles;
- Representative size measurement of particles with high aspect ratios;
- Validation of ensemble based particle size measurements such as laser diffraction.
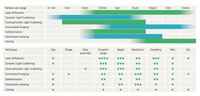
With an automated imaging system, statistically representative distributions are constructed from the individual images of tens to hundreds of thousands of particles in a single measurement. Such systems may be static, with a stationary dispersed sample, or dynamic, in which case the sample flows past the image capture optics. Both allow the user to visually examine a particle in exactly the same way as with a microscope, but they bring objectivity, high throughput and greater statistical rigour to image capture and analysis.
Today’s analysts have a wide range of particle characterisation tools at their disposal that includes a number of different technologies for measuring particle size, the most widely analysed particle parameter. Selection relies on a thorough appreciation of the data that each one generates as well an understanding of the practicalities of their application. Well-informed users are able to exploit the strengths of each method to gain the information needed to support successful formulation, development and manufacture.
Author: Carl Levoguer, Malvern Instruments
Contact:
t: +44 (0) 1684 892456;
f: +44 (0) 1684 892789