In a spin
11 Jun 2009 by Evoluted New Media

Just like a DJ working a club - when it comes to getting the perfect mix, it’s all about how you spin…
Just like a DJ working a club - when it comes to getting the perfect mix, it’s all about how you spin…
Mixing of materials in the laboratory or for smaller production volumes is traditionally done by hand, or the use of some sort of mechanical blade, impellor or paddle to agitate the mix. These are fine in their way - being largely inexpensive, manual or simple powered tool processes - and are adequate for many mixing tasks.
There are challenges when the materials involved include large differentials in viscosity, when one or more component is a very high viscosity, or when one or more components is a powder or other solid – in high technology applications, these could include organic materials, oils, aqueous solutions, clays, pastes, precious metal powders or nano-tubes. Critical applications may demand a guaranteed completely homogenous mix with no entrapped air, and a process which is both reliable and repeatable. Where materials are expensive or rare, process time and material wastage are also important factors, and mixing may be required in smaller volumes (i.e. less than 5g). Mechanical mixers can also damage fragile constituents.
Mechanical mixing techniques can be prone to introducing air into the material, which would be unacceptable for many applications, for example, an optical encapsulant. A separate and additional de-aeration process would then be needed - equipment to centrifuge or vacuum the air out of the mix. Usually vacuum degassing is a manual process which is time-consuming, messy and can result in foaming, leading to overspill of the material.
Clearly there ought to be a better way - and indeed an alternative approach is available using the principles of simultaneous rotation and revolution (planetary) motions, where the mixer equipment rotates the container holding the material and at the same time revolves the container. By simultaneously revolving and rotating, a strong whirlpool-type flow is generated in the materials themselves, stirring and dispersing them. By carefully altering the rotation and revolution speeds, and, crucially, the ratio between these movement speeds, flow currents are generated in the materials which are alone enough to completely mix the materials, without the need for any invasive mechanical stirrer. There is no air induced by this procedure - indeed, previously entrapped air in the materials is removed.
At Intertronics we have found that the Thinky planetary centrifugal mixers are capable of stirring with forces of up to 400g, which allows them to mix and disperse even high viscosity materials such as oil-based clay. This is made possible by programmable control of the various mixing gyrations. For example, the revolution speed can be adjusted to stir and disperse according to the material’s viscosity and mass. For materials that are sensitive to increases in temperature, the revolution speed can be lowered thus regulating the forces applied to the material. For high viscosity materials, the revolution speed can be increased thus applying maximum mixing force to the material, improving the quality of the mixing.
By altering the relative rotation and revolution motions, more centrifugal forces are induced into the materials, and degassing or de-aerating is achieved. It has been found that it requires 1000 rpm to mix well and at least 2000 rpm to degas well. If the container revolves at 1000 rpm and rotates at 1000 rpm (a 1:1 ratio), maximum mixing effects are seen, whilst a ratio of 1:2 at least is best suited to degassing. The optimal combination of these parameters can be chosen in a recipe for a mixing mode and a degassing mode for any material combination.
A programmable planetary mixer will allow both these mixing and degassing modes to be used in a timed sequence or sequences to give the best possible homogenous and air free mix. The Thinky AR-series enables changes in both the speed and spinning ratio under programmable control and can provide doubling of centrifugal force depending on the mode chosen in order to provide the best results and to suit specific applications.
It has been found that the degassing mode was sufficient for most processes, taking out air bubbles down to micron levels. However, as mixing requirements become more sophisticated Thinky have found that for some material combinations and to reduce time cycles for larger quantities, the addition of a vacuum environment within the mixer has improved degassing down to sub-micron levels as well as substantially improving process time.
An excellent example of using the planetary rotation process with a difficult to
Traditional methods have served for many years but mixers built on the rotation and revolution “planetary” principle are proving themselves excellent performers |
Alginic acid (Alginate) is a polysaccharide found in brown algae, red algae and coral weed - it is a common additive for food or elsewhere where it is used as a thickener/gelling agent/stabiliser or in cosmetics, dentistry, medical treatments, paper/textiles, fermentation and even in fibrous form as surgical thread. The pure alginate is fibrous, granular or powdery and insoluble in water which naturally complicates the mixing process.
In a simple back to back test a traditional manual mix of alginate and water in a 300ml container took 90 seconds. When solidified it was sectioned and showed excessive variation and many large air bubbles. A parallel process was carried out with the Thinky ARE250. The alginate and water in their container were put into the machine which ran for approximately 50 seconds. The result was a perfectly uniform mix consistency and no air bubbles, with complete batch repeatability.
The mixing of fine powders into thin liquids is prone to agglomeration, due to moisture and air entrapment effects. These may be overcome by the use of this type of equipment. A simple barium titanate ceramic/water mix can be seen to be mixed in two minutes with no agglomeration observed at x1000 magnification. Mixing carbon nano-fibres in epoxy has also proved problematical by traditional methods, largely because of the tangling or “wiring” of the fibres – however tests have shown that gentle progressive mixing generated by the planetary rotational motion enables the fibres to slide over each other in the substrate epoxy, so producing a homogeneous dispersion in a 15 minute operation.
Other test examples include nano-particles of carbon black in silicone, two part silicones, two part epoxies and optical application adhesives, potting compounds or sealants where inadequate mixing or the presence of air bubbles would lead to unacceptable visual distortions or other performance problems.
Clearly different industries have different requirements and in the laboratory we
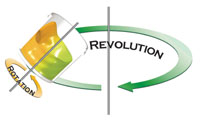
Once a successful mixing and degassing program or recipe is determined for a specific material, it can be called up at any time, thus making the process fully repeatable. Because the materials are mixed in their own container, material waste is minimised, there is no requirement to transfer materials from one container to another, contamination from mixing tools or special mixing vessels is eliminated and cleaning is very simple.