Avoiding common pitfalls deploying customised fume cupboards
23 Aug 2022
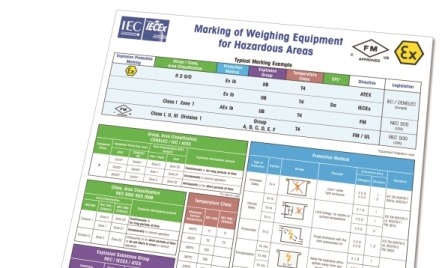
Fume cupboards are vital in an industrial setting but they need to be tailored carefully to the individual laboratory, explains Frank Hackett of TCS
Industrial fume cupboards play a crucial role in protecting people from hazardous substances. They offer vital localised exhaust ventilation when dangerous vapours, noxious dust clouds or unpleasant odours are a problem. They can also remove flammable fumes to help prevent explosions.
To be truly effective, however, industrial fume cupboards must be crafted to match the purpose they will serve. In teaching environments, such as a university, you are likely to see more basic design cupboards being used. But in industrial settings, the specific needs of the laboratory need to be taken into consideration.
In a research and development (R&D), quality assurance (QA) or containment lab, for instance, customisation will typically be needed to accommodate the exact chemicals and compounds being worked with. In pharmaceutical manufacturing, where fume cupboards need to slot into a production line, for a specialised process, you may also find a fully bespoke design needs to be deployed.
Engineers must ensure their fume cupboards are fit for purpose. And, if you’re working with a manufacturing partner to build new units, it’s helpful to know the steps involved and where the common pitfalls lie, so you can avoid them.
Match specifications to applications
All industrial fume cupboards need to be suitable for the activities taking place and the substances that are going to be present. If the end user is likely to be working with significant volumes of hydrofluoric or perchloric acid, for instance, handling will generally need to take place within a scrubbed inner chamber made from plastics or even a wet scrubbed extract system. Similarly, the handling of certain radio isotopes will require lead shielding around that inner chamber.
Whatever customisation is required, engineers need to ensure their requirements still mean the fume cupboards meet the BS EN 14175 standard. And, wherever solvents and flammable liquids are involved, organisations will also need to conduct a hazard and operability (HAZOP) study to ensure the fume cupboards complies with ATEX directives – as there will be the potential for an explosive atmosphere.
Understand ALL user requirements
It’s crucial that all stakeholders are consulted early – and that everyone’s requirements are understood and documented within a user requirement specification (URS). The last thing you want is to find that important considerations have been missed after placing an order. This can range from checking practical concerns, such as the electricity demands or what the control panel should show, to factoring in your organisation’s sustainability requirements.
If laboratories are looking to gain a competitive edge and attract top scientists with the best possible working environment, the need to customise is inevitable. Engineers should not be afraid to push boundaries
Consulting with users may lead to inclusive design changes such as creating a narrower or sliding sash or height adjustable legs. It’s worth asking whether options you may have thought impossible, are in fact achievable. For instance, if you want to wheel modular mobile skids in and out, you may need more than just a non-standard wider or taller unit. Can the baffle be fabricated to be removable? Can you find a manufacturer who can build units up to 3metres wide?
Try before you buy
Where any bespoke requests are being made, calculations will need to be made to assess the impact on containment performance – especially if airflow along the plane of the sash is likely to be disrupted. This may require the development of a fluid dynamics model to test what is possible.
However, before placing an order that may be worth hundreds of thousands, it is sensible to develop an initial 3D CAD model and then create a hard prototype so a full ergonomic review can be performed. This is not standard practice across the industry but the ability to experiment with these mock-ups is invaluable – and can make all the difference for operators. If a sash needs to be narrower or a tap moved lower, this prototype will reveal that requirement before it’s too late.
Conduct a site review
The environment around a fume cupboard can make a big difference to the performance of the unit. An over or under supply of air can severely impede the unit’s containment performance. This can be an issue when the room where the fume cupboard will sit is too small or where supply air diffusers are positioned too close to the unit.
To prevent environmental factors interfering with performance, a site review will be necessary to assess the heating, ventilation and air conditioning (HVAC) designs and the dimensions of the room. Be sure that this review is conducted by someone who is qualified to assess HVAC designs and understands the potential implications for fume cupboards. In our experience, this is one of the most common reasons for a unit not performing after having been commissioned.
Test thoroughly
Before going into operation, customised and bespoke fume cupboards will need to pass the appropriate tests. Engineers will need to demonstrate that their manufacturer has met the commissioning, qualification and validation (CQV) requirements – and should expect documentation and equipment databooks that show compliance.
A fume cupboard will also need to pass a factory acceptance test (FAT) to ensure the equipment works as intended and meets all specifications, as laid out in the URS. This will also include a site acceptance test (SAT), which will prove that the fume cupboard operates as expected in situ (e.g. it is not impacted by local environment factors, as mentioned above) and it is safe for operators to use.
Creating a best in class lab
It’s not unusual to see engineers trying to shoehorn off-the-shelf fume cupboards into industrial environments. They might be fortunate and find a standard unit that will do the job – but this is not something we would generally recommend.
If laboratories are looking to gain a competitive edge and attract top scientists with the best possible working environment, the need to customise is inevitable. Engineers should not be afraid to push boundaries and set high expectations for the performance of their fume cupboards. Creative solutions that are both fit for purpose and compliant are now achievable thanks to technological innovation.
Frank Hackett is Business Development Manager at TCS, part of Envair Technology