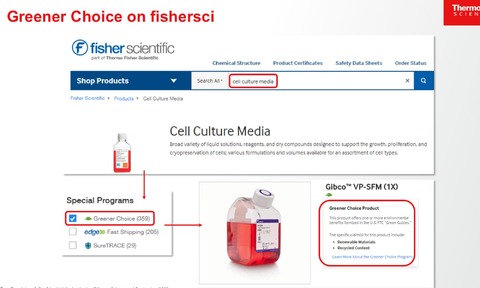
Sustainability was the core of Lab Innovations’ MyGreenLab/Laboratory News seminar series. In the first of a series looking back at some key talks, we report on Thermo Fisher Scientific’s contribution.
There are few businesses today that do not express a thought for climate change when updating their vision and mission statements. But the challenge, of course, is how to convert sentiment and utterance into practical and concerted measures.
Program Manager at Thermo Fisher Scientific (TFS) Jim Bratherton was one of the speakers at the two-day Lab Innovations sessions, hosted at the event’s Insights and Innovation Theatre and focused on sustainability and sustainability training in the laboratory environment.
Bratherton’s talk provided detailed insight into how one of the largest companies within its field seeks to make what he describes as a “positive, science-based impact”.
TFS aims to fulfil a long-term target of net zero emissions by 2050 – defined in accordance with SBTi (Science Based Targets initiative) emission reduction guidelines as an absolute reduction of at least 90% with permanent removal for equivalent amount of remaining emissions. To do so, it applied the standard three stage carbon accounting ‘scope’ framework: Scope 1 being those emanating directly from the business; 2, indirect but onsite and derived from powering facilities; and 3, those from external sources down value and supply chains, that ultimately derive nonetheless from TFS activities.
In order to help ensure fulfilment of its eventual goal, Thermo Fisher has set itself short-term targets just past the middle point of the road to 2050. For TFS scopes 1 and 2, this involves a 30% greenhouse gas reduction by 2030 measured against a 2018 baseline; for scope 3, ensuring 90% of suppliers set sciencebased reduction targets by 2027.
In broad terms, the practical aims of the different scopes break down thus: Scope 1 greenhouse gas emissions to be tackled with a transition from fossil fuel use; Scope 2 emissions, by the acceleration of renewable electricity adoption; Scope 3, by engaging with suppliers via the CDP and EcoVadis environmental disclosure and ratings systems programs.
Thermo Fisher Scientific’s own Sustainability Program focuses on net zero progress, no waste to landfill, and climate and ethics disclosure, as well as local environmental sustainability initiatives.
But, in addition, Bratherton has been responsible for the creation and management of two complementary initiatives that provide an opportunity to nudge suppliers and consumers towards greener practices.
The challenge, of course, is how to convert sentiment and utterance into practical and concerted measures
Of these initiatives, the Green Solutions toolkit helps enable customers to reduce their scope 3 carbon impact by providing greater visibility for a choice of more sustainable products, eco labelling, 100% recyclable shippers and lower carbon transportation options.
Under Green Solutions’ auspices, the second initiative, Greener Choice, showcases products on the website containing environmentally preferable products, denoted with an easily identifiable green leaf symbol, that provides up to 13 product claims aligned to US Federal Trade Commission Green Guides.
With an estimated 7,000 products making greener claims overall, the TFS website provides a filter for Greener Choice products; for example, a search for cell culture media highlights nearly 360 Greener Choices, each specifying with which green guide claims they align (renewable materials, recycled content, etc).
Within the TFS green product range, more than 500 carry the new ACT environmental impact factor (EIF) label. Pioneered by My Green Lab and popularly dubbed the ‘eco nutrition’ label, this translates the system of food nutrition labelling to a new arena. It scores each featured item under categories including manufacturing, user impact, end of life and innovative practices, then offers an overall EIF figure too. Not only a facility for the purchaser, said Bratherton, but a driver for suppliers, including TFS, to seek continuous and measurable improvement.
The process is further encouraged via the Greener Switch component of Greener Solutions, explicitly offering customers the chance to view alternatives that contribute to lessening the environmental impact of lab operations.
Transport logistics offer another chance to make inroads, via the Lower Environmental Impact Delivery that provides consolidated and scheduled shipments, alternative routes and pre-determined dispatch days.
Waste too forms a key part of the equation, both through recycling and reduction on site and by influencing customer behaviours.
Within the UK, TFS waste collection handles glass, plastic, cardboard and PPE, supplemented by partnerships with Kimberly- Clark RightCycle and TerraCycle. Additionally, there is optimised recycling at TFS European distribution warehouses, while 24 sites are certified zero waste to landfill – ensuring more than 90% of TFS waste overall is diverted from this option.
Having launched itself on the road to a more sustainable future, what has TFS achieved to date? Quantifying results can be a fraught undertaking when the work is conducted as an internal exercise, hence the interest in applying externally-created measurements such as ACT labelling provides. Consistent with this approach, the company also sought impartial validation of its approach, submitting its list of goals to SBTi in June last year, outlined Bratherton. To date, he said in November, the company had achieved:
- Absolute emissions decrease of 12% since 2018, making it possible to exceed the 2030 target of 30% reduction
- Energy assessments at 45 sites worldwide, US$20m funding of green infrastructure
- Governance for TFS climate program at board level
- Increase in renewable electricity 22% (58% in Europe) from 15% in 2020
- And is on course for tripling of onsite solar in the next 2 years.