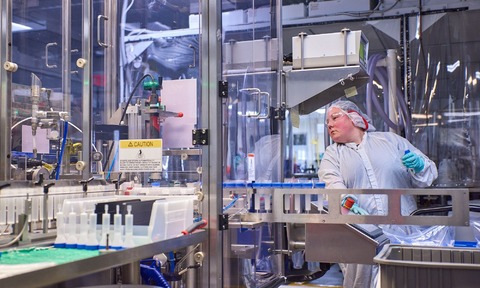
Sustainability, market pressures and tech innovation are impacting the chemicals and materials sectors. ‘Sweating the assets’ and maintaining compliance has consequences for the laboratory too, explains the Chemical Industries Association Head of Innovation and Events Mike Lancaster.
As the Chemical Industries Association admits, its sector is at best a cautious endorser of automation and digitisation. For the SMEs who comprise the majority of its members, the capital required and the length of return on investment make a sometimes questionable business case for rapid adoption.
External factors, however, are contributing to the need for evolution. Economic pressures have ratcheted up; likewise regulatory, supply chain and environmental demands. Simultaneously, innovative instrumentation and systems have become potentially more affordable.
Two complementary sectors – materials and pharmaceuticals, as well as their academic counterparts – are noticeably active on these fronts. In Liverpool, for example, the Leverhulme Research Centre is pursuing the goal of harnessing computational design for the prediction of ‘experimentally realisable crystal structures and properties’ and complex systems that mimic biology.
Meanwhile, in industry, firms such as Optimal Industrial Technologies are employing Process Analytical Technology (PAT) to enable smart, automated and process control approaches for challenges such as solid mixing, using real time measurement to determine material and quality attributes. Several years ago McKinsey & Co’s Digitisation, automation and online testing: The future of pharma quality control asserted an average chemical QC lab could reduce costs by 25% to 45% via digitisation, with substantial savings in manual documentation and investigation workloads. It noted that “digitally enabled labs also reap complianceimprovement benefits from reduced errors and variability, as well as seamless data retrieval and analysis”.
Distributed control together with digitisation and automation offers the potential to embed the lab more fully in the production process, operating ‘at line’ rather than end of line. Laboratory News asks the CIA’s Mike Lancaster what implications are there for the lab in the industrial context?
The future development of chemicals production is described as dependent on a trio of factors: automation, digitisation and distributed control. Do you think the latter one is often overlooked?
Distributed control systems (DCS) have been widely employed in chemical production for many years, with systems gradually becoming more sophisticated. It could be argued that it is the automation and digitisation aspects that have been lagging in the sector. It is true that many companies are probably not making full use of the capabilities modern DCS systems offer, because of the lack of automation and digitisation. There are many reasons for this including the perceived cost benefit, with a lack of case studies for the sector and concern over cyber security as systems become more automated and ‘connected’.
Real Time Response Testing (RTRT) and Process Analytical Technology (PAT) are seen as key to the development of distributed control. What is the business case for their adoption in the chemicals and materials sectors?
PAT came to prominence in the pharmaceutical sector around 20 years ago when the aim of the [US] FDA was to minimise the risk to public health of pharmaceutical manufacture, by ensuring every batch of product was as identical as possible to the standard batch. For most chemical manufacturing processes such tight control is not essential, although it is desirable.
RTRT is a key aspect of PAT and instrumentation has developed from traditional sensors such as temperature, pressure, pH, density and conductivity to include more advanced and expensive techniques such as online IR, near-infrared (NIR), Raman, UV-vis, mass spectroscopy etc.
While the business case for installing these on-line can be made for many pharmaceuticals on the basis of regulation, the cost of raw materials for lost batches, equipment downtime etc, the business case in chemicals manufacturing is less clear cut. It is a cost benefit question that will be different for each product.
However, as the relative cost of online instrumentation reduces and productivity and process efficiency become more important and it is essential to ‘sweat the assets’ to remain competitive with lowercost products from China, the Gulf and the US, RTRT is becoming more common, particularly in bulk chemicals manufacture.
Combining RTRT with the latest DCS systems should lead to significant productivity and efficiency gains as well as potentially improving energy efficiency, which is now vitally important both for the bottom line and as a pathway to Net Zero.
These control processes will impact lab operations within industrial contexts. Is the intention to remove many lab functions performed towards the end of the process and embed them within the production process? Likewise, from the physical, manual sphere in favour of online and virtual activity?
Undoubtedly RTRT, automation and digitisation will change the way chemicals are manufactured and tested. Some lab functions, mainly in-process testing, will be embedded into the process and in many cases the chemicals will not need to come into contact with humans until the end of the process. There will be many opportunities in the lab to develop processes that can be automated and to use QC analytical techniques that can be implemented online.
Does this imply a more restricted role for the traditional laboratory? If so, what functions and responsibilities would it retain?
The traditional QC lab has changed significantly over the years. We have seen QC labs operating 24 hours a day, staffed with specialists for each analytical technique, gradually move to only being staffed by specialists on day shift with plant operators being trained in more analytical techniques to do on night shift to basic analyses being performed at-line to get a faster response.
Online testing is the next step in this evolution and will save huge amounts of time and lost batches by avoiding taking samples, walking them down to the QC lab and waiting for the results with the batch on hold often for several hours. The QC lab will still have a very important role to play both in final product testing and troubleshooting when things go wrong and more detailed analyses and interpretation of data are required.
Investment in innovation can bring big returns but it certainly involves large costs. That can’t augur well for many SMEs, surely? Are too many firms rushing to automate without having a coherent business case for investment?
I think we need to differentiate between automation and more widespread innovation. SMEs have an excellent record of innovation. Indeed, innovation is often critical to the establishment of start-up companies in the sector. For a new plant, the difference in cost between a well-automated plant and a more traditional plant requiring more input by people is often not that great. It is more difficult to add automation to an old plant. Many SMEs with older plant will be producing niche products with little competition or in general-purpose batch equipment used for making several products. Making a coherent business case for automation in these cases may be difficult and it may well be that the SME can continue making many chemicals profitably without automation.
Some lab functions, mainly in-process testing, will be embedded into the process and in many cases the chemicals will not need to come into contact with humans until the end of the process
The chemical industry is relatively conservative and indeed many would argue that it has been slow to adopt automation and digitisation rather than rushing to implement them. With few exceptions, the chemical industry will be looking for a payback of one to two years for this kind of investment. It is often the capital cost combined with some degree of uncertainty as to the benefits which hold companies back.
As in many sectors, computational modelling is offering new refinements in chemicals and materials science. How will this manifest itself in areas such as the development of chemical reagents?
Historically the synthesis of new chemicals and materials has been relatively timeconsuming, expensive and wasteful of resources with significant amounts of solvent and reagents requiring disposal. Computational or molecular modelling gives scientists the ability to streamline this process, cutting the development time required and contributing to the sector becoming more sustainable.
As models become more sophisticated and Big Data more widely available and used, we should see the cost and timescales of chemical and material development cut further, which should mean more new products coming onto the market faster.
Mike Lancaster is Head of Innovation and Events at the Chemical Industries Association