Pines and paper alleviate science's sustainable pain killer headache
9 Jul 2023
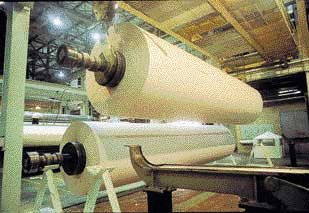
Bath University's Department of Chemistry and Institute for Sustainability has revealed a sustainable alternative to the use of crude oil for producing pain killers including paracetamol and ibuprofen.
They have harnessed turpentine – a compound found in pine trees and a waste product from the paper industry – to create the products.
Pharmaceuticals have relied traditionally on chemical precursors derived from crude oil, a dependence that has become a sustainability issue, given efforts to achieve Net Zero.
The new approach employs biorenewable sources, specifically making use of some of the 350,000 tonnes of turpentine generated annually as a waste by-product generated in significant quantities.
This can provide the sustainable starting material for a range of chemical applications including pain killer production.
The researchers focused on β-pinene, a key component of turpentine, and successfully converted it into paracetamol and ibuprofen on a large scale, reaching production levels of around 100,000 tonnes annually. They also synthesised other precursor chemicals from turpentine, including 4-HAP (4-hydroxyacetophenone), which serves as a building block for drugs like beta-blockers, salbutamol—an asthma inhaler medication—and various perfumes and cleaning products.
Not only does this potentially reduce chemical industry dependence on oil extraction, thereby mitigating rising CO2 emissions, says the research team, there is also a geopolitical benefit; turpentine's availability is not affected by the stability of oil-reserve-rich countries, thus avoiding the effects of price fluctuations associated with crude oil.
Dr. Josh Tibbetts, Research Associate in the Department of Chemistry at the University of Bath, explained the need for sustainable alternatives: "Using oil to make pharmaceuticals is unsustainable—contributing to rising CO2 emissions and subject to dramatic price fluctuations. Instead of extracting more oil from the ground, we want to replace it with a 'bio-refinery' model."
In this model turpentine is employed to produce a diverse range of sustainable chemicals. This not only offers a more environmentally friendly option but also through continuous flow reactors, enables uninterrupted production and easier scalability compared to batch-based reactors, say the researchers.
One disadvantage remains cost, as the current price of the process is higher than that for oil-based feedstocks. However, the Bath team suggests consumers and Governments that prioritise sustainability may be willing to pay the higher price in order that pharmaceutical production aligns with the increasing global demand for environmentally conscious solutions.
The research findings have been published in ChemSusChem and the work was supported by funding from the Engineering and Physical Sciences Research Council.