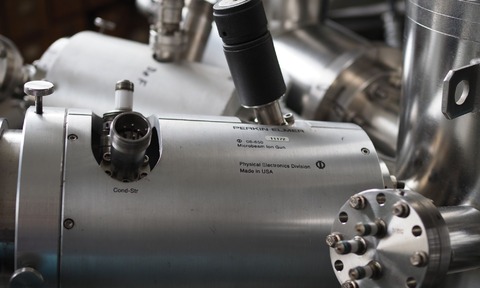
Scanning electron microscopy (SEM) plays a crucial role in engineering advanced materials but accurate results require careful sample preparation and transport, advises Britta Siefer.
Across industries, scanning electron microscopy (SEM) is unlocking breakthroughs by providing a deeper understanding of the structural and chemical properties of materials.
For instance, in battery research, SEM characterisation of lithium-ion (Li-ion) battery materials is used to assess the quality and composition of the produced cathodes and anodes. If the sample surface is prepared to a high standard, it is possible to identify physical characteristics in the cathode layer, such as layer thickness, particle size, particle crystallography, particle cracking and porosity. These characteristics can directly impact the performance, capacity and lifespan of batteries. Equipped with these insights, researchers can optimise materials, ultimately leading to the development of more efficient and durable energy storage systems.
However, the success of SEM analysis hinges on maintaining sample integrity throughout preparation, handling and transport. Airsensitive metal alloys and materials such as lithium are highly reactive and vulnerable to degradation during these stages, making a controlled, consistent workflow crucial for achieving uncompromised results.
Preparing without contaminating
The preparation process is crucial to ensure accurate imaging results, as many advanced SEM techniques – such as elemental dispersive spectroscopy (EDS) and electron backscatter diffraction (EBSD) – demand smooth sample surfaces.
Yet, the preparation phase itself can introduce contaminants or create surface irregularities, both of which can impede the analysis of microstructural features. As a result, the data produced may be unreliable or incomplete, undermining the accuracy of the SEM analysis.
Mechanical polishing has long been a standard method, but it comes with drawbacks. Using abrasives such as fine sandpaper, mechanical polishing effectively smooths the sample surface, though it also creates surface damage in the form of scratches, smearing and distortions. Damaging the sample surface in this way results in critical characteristics such as grain boundaries, phases and nanoparticle distributions being obscured.
The preparation of composite materials is particularly challenging. These materials often consist of multi-phase structures, combining components such as metals, ceramics and polymers, each with different physical properties. Cutting these materials improperly can cause delamination or alterations in the microstructure, potentially distorting the phases within the material. The need for precise, controlled preparation techniques is even more critical in these cases, as the integrity of each phase must be carefully preserved.
The benefits of ion milling
Ion milling addresses these challenges by providing a means of preparing the sample surface without damaging it. Unlike traditional mechanical polishing, ion milling uses a focused beam of inert gas ions to gradually remove surface layers without creating heat or physical stress. This results in a smooth, clean surface ideal for advanced SEM techniques like EBSD and EDS.
The key advantage of ion milling is its precision. The ion beam can be finely controlled to ensure a consistent surface without the mechanical stresses that can distort delicate samples. In addition to sample preparation, ion milling systems can also be used to create clean, well-defined crosssectional samples. This capability is essential for studying thin films, composites or la yered materials in greater detail.
Furthermore, ion milling minimises the risk of contamination that may arise from polishing with external materials, as the process is entirely controlled within an argon environment.
Sample transport integrity
Preparing samples effectively is crucial but it is meaningless if they are not transported to the SEM properly. Even the most carefully prepared samples can be jeopardised during transport, particularly if they are highly delicate materials. For example, aluminium-lithium (Al-Li) and nickel-based superalloys that are often used in aerospace applications can be extremely air-sensitive. For these materials, exposure to air can cause oxidation or hydration, which are damaging to the sample surface.
The preparation phase itself can introduce contaminants or create surface irregularities… As a result, the data produced may be unreliable or incomplete, undermining the accuracy of the SEM analysis
To combat this, vacuum chambers are often used during the transport stage. However, non-automated transfer systems do not always provide sufficient protection for such reactive materials. These systems are typically incapable of consistently monitoring and controlling environmental factors such as temperature, humidity and gas composition. Without precise regulation, even slight changes in these factors can cause degradation to the sample surface, preventing accurate analysis. As a result, the sample preparation process may need to be repeated, wasting time and resources.
For reliable, repeatable results, automated transfer systems are key. Many of these systems use an argon environment to maintain control over the conditions during transport, ensuring that samples are protected from the damaging effects of oxidation or hydration. This not only improves the accuracy of analysis but ultimately also enhances efficiency by eliminating the need for repeated sample preparation.
For example, Thermo Fisher Scientific’s microscopy solutions include the Red Dot Design Concept Award-winning CleanMill Broad Ion Beam System, which integrates with the Inert Gas Sample Transfer (IGST) Workflow for sample preparation and transport.
When analysing and engineering materials on a microscopic scale, every detail matters. Since samples can so easily be damaged or compromised during preparation, handling and transport, it’s crucial to establish a reliable workflow. By using advanced methods such as ion milling and ensuring controlled transport conditions, researchers can preserve sample integrity and obtain accurate, repeatable results that could lead to breakthroughs in materials science.
Britta Siefer is senior sales account manager – industry, materials science at Thermo Fisher Scientific and studied chemistry at the University of Essen