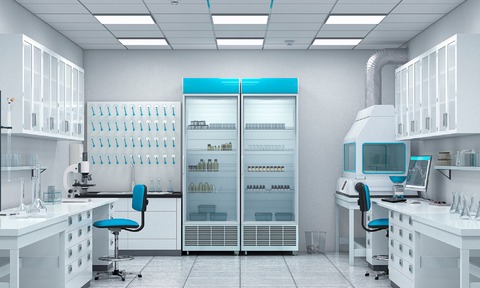
Product and marketing manager at leading lab furniture and equipment designer and manufacturer Teknomek Michelle Locke discusses the changes and challenges of catering for the sector.
What trends are you seeing in demand for stainless steel lab furniture and equipment – and how is Teknomek adapting?
Teknomek has been designing and manufacturing stainless steel furniture and equipment for environments where hygiene is critical for more than 40 years, however that’s just part of the picture. We provide a complete solution, with a managed catalogue of products that is constantly evolving to meet the changing needs of the industries we service. We never stop listening to customers and adapting our services and product range accordingly.
With hygiene protocols in research and clinical environments becoming ever stricter, customers need furniture and equipment that supports both operational and regulatory standards.
There’s also a growing emphasis on sustainability and ergonomic design within the pharma sector.
While the demand for highly durable, hygienic and customisable stainless steel lab furniture continues, in laboratories white, powder-coated steel furniture is popular. Powder coating steel not only builds a barrier between moisture and humidity, but the white surface reflects light, enhancing visibility in the laboratory and creating a clean, professional appearance.
The coating provides resistance to many laboratory chemicals, preventing degradation from spills and ensuring long-term usability.
Teknomek is innovating around these trends. We utilise products such as Trespa and Sealwise, both exceptionally hygienic materials, providing customers with a wide range of options, in addition to stainless steel.
We are also seeing a significant increase in bespoke orders, evidencing the fact that our customers in the pharma sector are investing in specialist, customised hygienic equipment that plays an active part in GMP (good manufacturing practices).
How do you ensure products meet both regulatory and environmental sustainability standards?
We maintain stringent compliance with key regulatory standards, such as ISO 9001. For environmental sustainability, we continuously evaluate our sourcing strategies to prioritise recyclable and low-impact materials such as stainless steel. Additionally, we invest in energyefficient production technologies and work with suppliers who share our commitment to responsible manufacturing.
For example, our relationship with Sealwise meets all our criteria for professional partnerships. Sealwise Waterproof Construction Board (WCB) products are manufactured in the UK and provide customers with a waterproof, durable and anti-bacterial solution. Sealwise WCB is also an environmentally responsible material. It is made from PVC which, due to advances in recycling processes, is viewed as one of the greenest materials available because it can be recycled multiple times. The outer top and bottom surface of Sealwise WCB is made from virgin PVC and the core of the board is made from recycled UPVC.
What innovations has Teknomek introduced in lab furniture design that improve efficiency or hygiene in controlled environments?
Our designs always emphasise cleanability and contamination control, with features such as seamless welding, rounded edges, sloping tops on storage items and minimal dirt traps. For ultrasterile environments our designs consider the combined role of HVAC and furniture design on air particle management. We’ve also developed modular, configurable furniture systems that allow for flexible lab layouts. The majority of our furniture can be mobile, with the addition of hygienic castors, for even more ease of use.
To mitigate supply chain risks, we’ve diversified our supplier base and built strong relationships with both domestic and international partners. We also maintain strategic stock levels of critical materials
Innovations like integrated storage solutions, height-adjustable workstations and antimicrobial coatings enable our customers to enhance both hygiene and workflow efficiency in controlled environments.
For ultra-sterile workspaces, such as A&B grade cleanrooms, our Hygienox range, made from 316L-grade stainless steel, and with the option of electropolishing, provides furniture that is robust enough to withstand pitting and corrosion from even the harshest of chemicals.
Stainless steel’s durability and hygiene benefits are obvious, but is it a challenge to balance this with cost-effectiveness, given yours is a competitive market?
While stainless steel is an upfront investment, its quality, durability, hygienic benefits and lifetime value outweigh the initial cost. Because we have advanced design and manufacturing capabilities in house, we can produce bespoke stainless steel furniture and equipment for customers to meet even the most complex of challenges.
We ensure cost-effectiveness by optimising our designs to minimise waste and production costs without compromising on quality. By improving efficiency in manufacturing and offering tailored solutions, we help clients maximise their budgets and productivity.
How closely do you work with lab professionals to customise products to meet specific research and clinical environment needs?
We always collaborate closely with our customers and their lab professionals from the very start of a project.
It means we can produce tailored solutions so they are completely perfect for purpose; helping businesses to optimise their workflows, reduce cleaning times and ensure effective risk management.
Our customer feedback process also ensures continuous improvements and innovations that address real-world challenges such as ergonomic design to ensure staff wellbeing and the need for work-space flexibility.
Are you exploring alternative materials or coatings to enhance antimicrobial properties or chemical resistance in lab furniture?
We are continually researching new technologies to enhance our product range and own manufacturing capabilities.
As previously mentioned, white furniture is always popular for customers wishing to create a light, streamlined, hygienic-looking laboratory space. We offer Trespa TopLab Base and TopLab Plus. TopLab Base is ideal for environments where durability is key but chemical resistance is not critical. TopLab Plus offers the added benefits of 24-hour chemical resistance and anti-bacterial protection.
Our Sealwise WCB products are made from fully waterproof, not just water resistant, construction board. WCB utilises its own Sealwise Protect technology to provide fast, effective and longlasting anti-bacterial protection which cannot be removed however rigorous the cleaning or wear and tear, making it ideal for laboratories. The treated surfaces inhibit bacterial growth and reduce odours, making furniture constructed from WCB vastly more hygienic and durable than wood-based construction boards such as MDF.
Various supply chain crises have affected most firms’ ability to source raw materials: what steps have you taken to counter these challenges?
To mitigate supply chain risks, we’ve diversified our supplier base and built strong relationships with both domestic and international partners. We also maintain strategic stock levels of critical materials, including stainless steel, to reduce lead times and ensure consistent supply. Additionally, we’ve streamlined our production scheduling to improve flexibility in response to fluctuations in material availability.
To what degree do you invest in UK-based manufacturing or sourcing to improve supply chain resilience and reduce lead times?
Investing in UK-based manufacturing and, wherever possible, local sourcing is a core part of our strategy. This allows us to maintain control over quality, reduce transportationrelated delays and respond quickly to customer needs. By supporting UK suppliers and enhancing our in-house capabilities, we continue to strengthen our supply chain resilience and deliver on shorter lead times.