New lab... but is it operationally ready?
7 Jul 2024
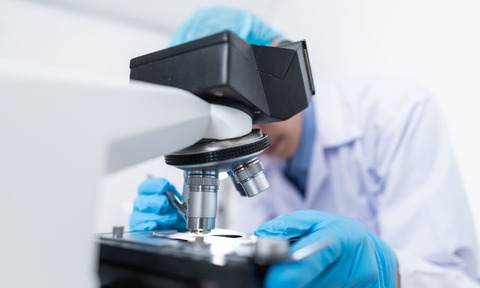
Lab space may be in short supply but don't neglect any element of the moving in process, urges Tes Adamou: the first step on arrival should be achieving the best state of operational readiness...
When you get a new kitchen, the layout and equipment chosen reflect how it will be used – you don’t want cooking utensils stored far away from the hob, for example.
Similar planning applies to laboratories, but it is just one of a number of considerations in getting new facilities operationally ready.
Taking a facility from the completion of the building works to a state where science can be carried out is a complex process that requires careful planning.
In-house staff will, naturally, be focused on what happens on site once it’s operational, but delivering operational readiness requires extra resources and plenty of time.
Taking a facility from the completion of the building works to a state where science can be carried out is a complex process that requires careful planning
Smaller businesses are unlikely to have an in-house facilities team with the appropriate capacity to deliver the extra work required. It’s more involved than having a project manager liaising with scientists.
Delivering for laboratory space includes a variety of processes, from equipment commissioning to quality assurance and training. It requires the input of pretty much every team within the business, from scientists to the legal department and IT.
The Quality Assurance (QA) processes tend to be on the critical path because of the amount of work involved, often leading to a bottleneck. It requires a much heavier input that typically the resources of a QA team at steady-state cannot resource.
With their day-to-day job, QA teams tend to need to double in size (whether internally or externally resourced) to carry out the extra work needed to get the facility operational.
Identifying the right people who understand the business sufficiently should be part of the initial planning process in which the different departments' workstreams are plotted out.
Assigning team leaders the appropriate autonomy to put their operational readiness delivery programme together can be an effective strategy. Understanding the different operational drivers and adopting processes early can avoid problems later on.
Sustainability targets are a good example. There may be legal or funding requirements to report on things like operational carbon to meet environmental goals. However, you can’t report without benchmark data recorded from the outset.
In-house staff will, naturally, be focused on what happens on site once it’s operational, but delivering operational readiness requires extra resources and plenty of time
Equipment management is another area where it is critical to understand the requirements and steps to take early in the process to deliver timely operational readiness.
Whether installing new equipment or moving equipment from an older facility to a new one, the most important document during this phase of laboratory set-up is the equipment list. This should not only identify what the equipment is, but also the requirements for calibration, commissioning and qualification.
This way, all the steps from selection and procurement through to qualification can be appropriately scheduled, and resources can be identified.
For manufacturing equipment under GMP, the qualification process is very prescriptive and requires extra layers, from writing protocols to undertaking the qualifications and identifying a representative load for each equipment. In some cases, both existing and new equipment may require comparability studies to ensure consistency of results.
Engineers who can move, calibrate and certify equipment are generally in very high demand. With availability that ranges from weeks to months, they need to be identified and booked well in advance.
Procuring new equipment is equally time-consuming, with approval processes and delivery times to navigate, particularly if it comes from abroad and has to go through customs.
The order in which equipment is installed, if carefully planned, can help with other stages of delivering operational readiness. For example, undertaking the qualification of a new fridge or freezer in a lew laboratory first means they can be used to store materials that might be needed for qualifying other equipment.
Integration of new with existing laboratory equipment also needs to be considered in the planning process, as well as how new equipment works with existing software.
Going back to the kitchen analogy, the position of each piece of equipment and how it relates to the specific work being undertaken should be considered. Is everything in a logical and accessible place?
Get team leaders and operators to demonstrate how they work, such as “Where would you look for gloves?” or “Where would you put X or Y?” That will help determine where everything in the laboratory goes and make the production process much smoother further down the line.
A key learning to any project manager for laboratories is to start giving responsibility back to key personnel gradually. A soft landing during operational readiness helps empower team members and puts them in a good position when the facility goes live.
With the right planning and resources, you can avoid delays in operation and help support ongoing lab work.
Pic: Chokniti Khongchum
Tes Adamou is CEO of EEDN and chair of the Constructing Science consortium, which published the Operational Readiness Report for laboratory science facilities.